The Proof is in the Performance
Giving Fresh Life to SDSU’s Wagner Hall
Originally built in 1969, Wagner Hall has been known by many names and housed multiple programs at SDSU. The building was opened as Home Economics and Nursing (HEN) before becoming the Nursing, Fine Arts, and Arts and Sciences Building (NFA). As Wagner Hall, the space is now home to several different colleges, including the College of Nursing, Education and Human Sciences, and College of Arts, Humanities and Social Sciences. While the programs within its walls have changed throughout the years, the building itself – offices, classrooms and labs – has remained a centerpiece of campus.
Since the building was constructed in 1969, barring a few limited renovations, the original mechanical and hydronic equipment has remained in service. The heating, ventilation, and air conditioning is supplied by two large air handling units (AHU) with variable air volume (VAV) boxes for individual control. The building is served by two AHUs, each serving areas with exterior exposures and interior spaces. In each air handler there are chilled water coils that cool the air. After the air exits the AHU, there are two sets of heating coils that heat it – one set serves interior rooms while the other serves rooms with exterior exposure. Also, the VAV boxes serving rooms with exterior exposures have hot water reheat coils. The building previously had a pneumatic controls system tied to the campus-wide building automation system (BAS).
In the late 1960s, the system was cutting-edge and allowed individual control in every room of the building. Originally, all the VAV boxes were shutoff-only boxes that didn’t have a motorized damper to modulate the airflow to meet the room demand, but could only open or close the pneumatic damper to either supply full airflow or no airflow to the space. Also, the initial air balancing for the VAV boxes was done with a factory preset spring that would only open enough to allow the required air into the space. But after years of service, the springs in the VAV boxes began to fail open so there were many spaces that were receiving 100 percent airflow even if the space was not calling for heating or cooling. Additionally, because the VAV boxes were shutoff type, as VAV boxes closed when spaces were satisfied, the supply air would bypass from the supply side of the built up air handling unit into the return of the air handling unit via a bypass damper located within the unit itself.
With this system, the AHUs were required to run at full capacity nonstop, which used excessive energy. At some point between the original construction and 2018, variable frequency drives (VFD) were added to the supply and return air fans to modulate fan speeds based on duct static pressure to help match the required airflow and reduce energy usage. But eventually, even these VFD’s began to fail and the system was switched back to constant volume. Additionally, over time, the pneumatic control lines plugged, which would cause spaces to lose control.
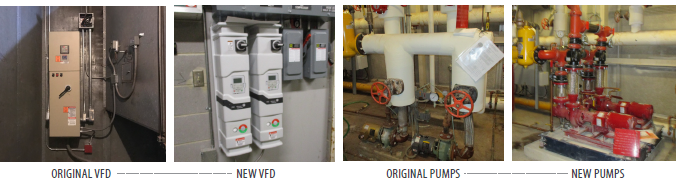
Given the age of the controls system, the VAV boxes did not have the ability to be monitored on the BAS so the only way the owner knew there was a problem with the system was a complaint from an occupant. In addition to the air handling units running full capacity at all times, the hot water pumps were not controlled by system pressure, so the pumps would run full volume nonstop as well.
Clearly, many aspects of the existing system were failing with age. The main goal of this project was to replace the aging temperature controls system, replace the VAV boxes that had outlived their useful life, and reduce the energy usage of the building.
Initially, the existing shutoff VAV boxes were replaced with modulating airflow shutoff boxes with digital controls and hot water reheat to better meet space heating or cooling needs. To lower the fan energy for the air handling units, the existing variable frequency drives for the supply and return air fans were then replaced with new VFD’s that were both physically smaller and had additional control points for BAS monitoring. Next, VFD’s were added to the hot water pumps to allow the pumps to be controlled by system pressure instead of running full speed constantly.
The largest portion of the project focused on helping reduce energy usage in the building. This involved replacement of the temperature controls system. All the pneumatic controls were removed from the building and replaced with a Direct Digital Controls (DDC) system. This included digital controllers for the VAV boxes, adding building static pressure sensors to control the supply and return air fan speeds, and a hot water pressure sensor to control the speed of the hot water pumps. Using a new controls system that could monitor building static pressure, the BAS system could review the damper position of all the VAV boxes in the building and lower the pressure until the appropriate number of VAV dampers were 100 percent open while still meeting the heating or cooling requirements of the various spaces. This in turn reduces the fan speeds and saves building energy.
The controls for the hot water system were similar to the heating and cooling system. A pressure sensor was added on the second floor, at the farthest point from the hot water pumps, that monitored system pressure. The speed of the hot water pumps was reduced to the lowest point possible while still meeting the heating requirements of the building. Ultimately, the new controls system both eliminated wasted energy due to equipment either running at 100 percent capacity when it wasn’t needed, or failed controllers that didn’t allow the owner to monitor which spaces were satisfied and which needed additional heating or cooling to match loads with capacities. The new controls also allow the owner to add many additional controls points to monitor what is happening in the building, eliminating wasted energy and identifying problem areas without relying on occupant complaints.
When all is said and done, the renovations to the systems within Wagner Hall improves occupant comfort, makes the facility easier to maintain, and enhances energy savings. The proof is in the performance. From September 2019 to May 2020 the owner saved 240,990 kWh of electrical consumption and 1,672,982 lbs. of steam over previous years in the building – giving Wagner Hall fresh life within its storied walls.
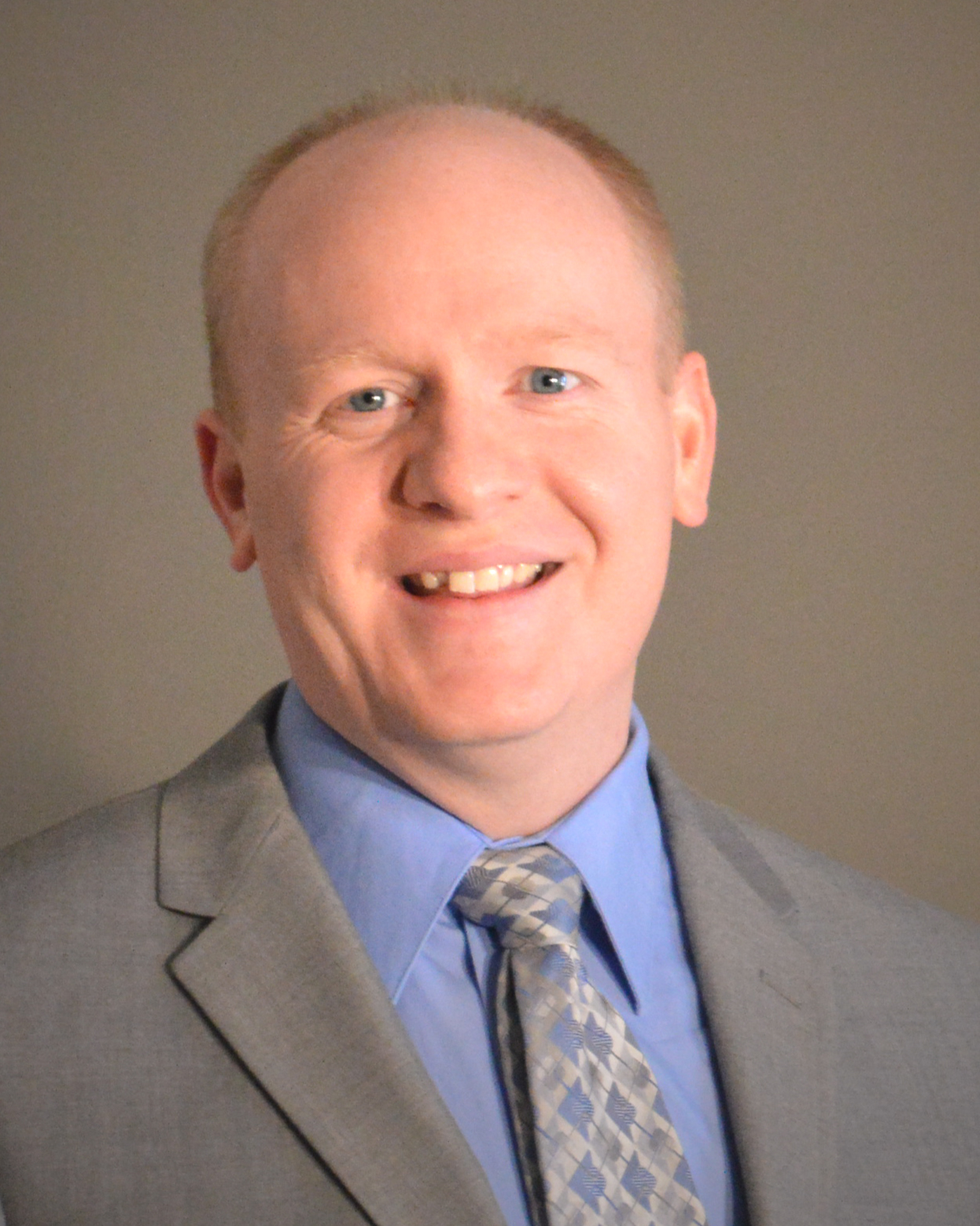
Isaac Anderson, P.E., is a Mechanical Engineer in the Sioux Falls office of West Plains Engineering. He has been with the firm 12 years, and was the Lead Mechanical Engineer and Project Manager for the Wagner Hall renovation project.